 |
Scan, trace, cut out, curse. Repeat |
 |
Finalized for waterjetting. |
|
| |
 |
Back from waterjetting |
Water jetting is a time saver when it comes to fabricating custom mounts, so long as I remember to double and triple check hole alignment and clearances. And, while water jetting is precise to 5 thousandths of an inch, it is not as precise as say, laser cutting, and things can skew slightly when cutting extremely thick material. For my purposes, though, it is a time saving device for the right price. While water jet pieces do need some cleaning up, its something I expect to do on all my bikes, since I sandblast and powder coat just about everything anyway.
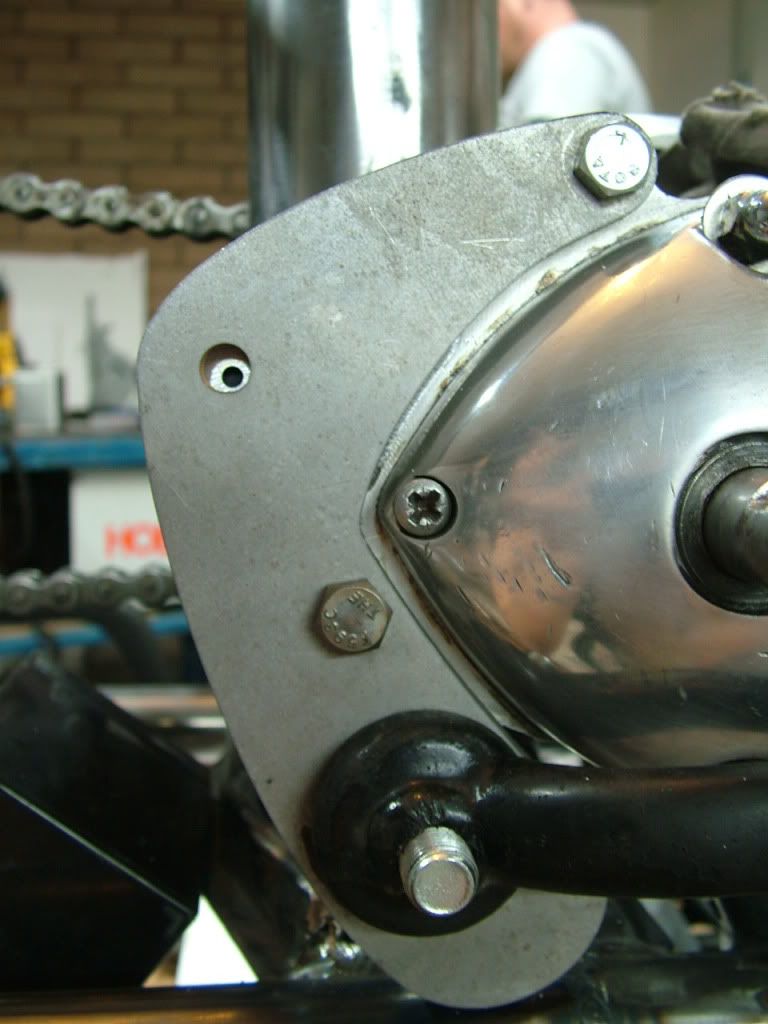 |
Cleaned up and mocked up |
When making these, I knew I wanted a shape that was graceful and would fit my aesthetic, while still having enough meat to support stress on the mounts. Because the stock mounts have more attachment points, cutting these to the standard thickness can make them slightly queefy when under stress.
To combat this tendency, these were cut out of 3/16" cold rolled steel, and I added an extra mounting point directly to the lower frame. Since I was still fabricating said mounting points when these went to the water jetters I left those and the tabs on the frame undrilled.
Which turned out to be a good thing. It meant that all I had to do was throw the mounts back in, drill holes though both pieces, and enjoy my new rock solid motor mounts.
We do have these for sale, 50 bucks a pair including shipping to the lower 48, in raw form, straight from the water jetters. Stainless is an option, as are different thicknesses, contact us for a quote.
 |
Clean looking, and nigh indestructible. |
 |
Powder coated and installed |